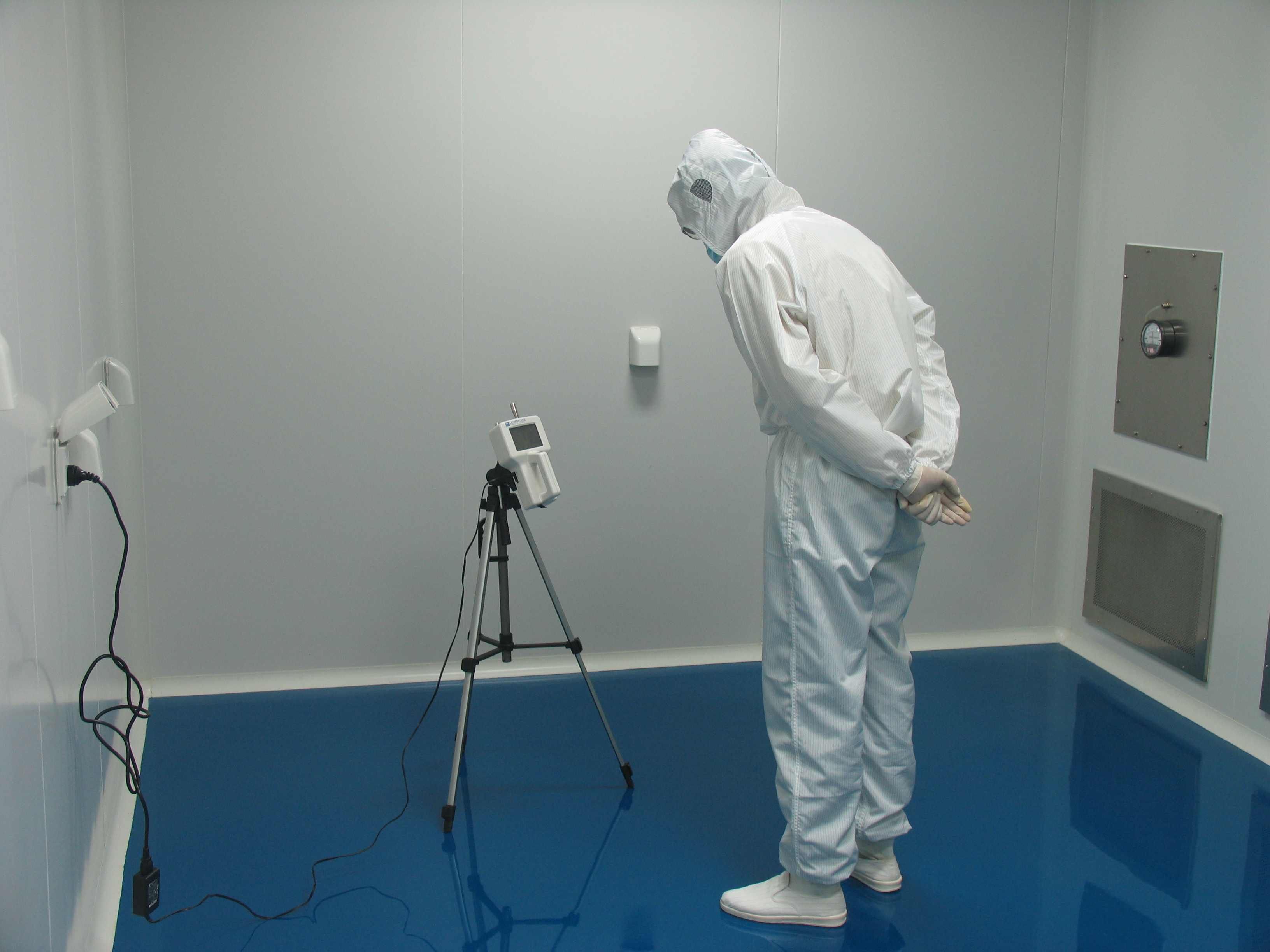
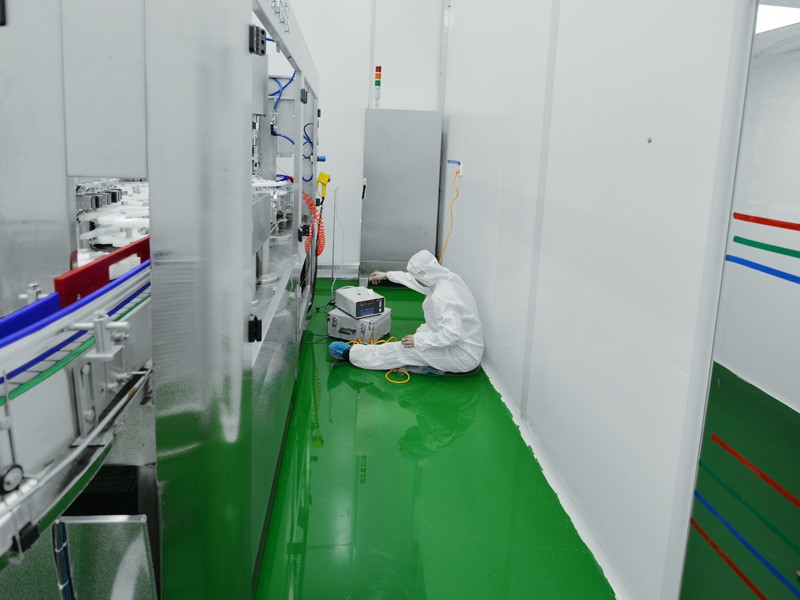
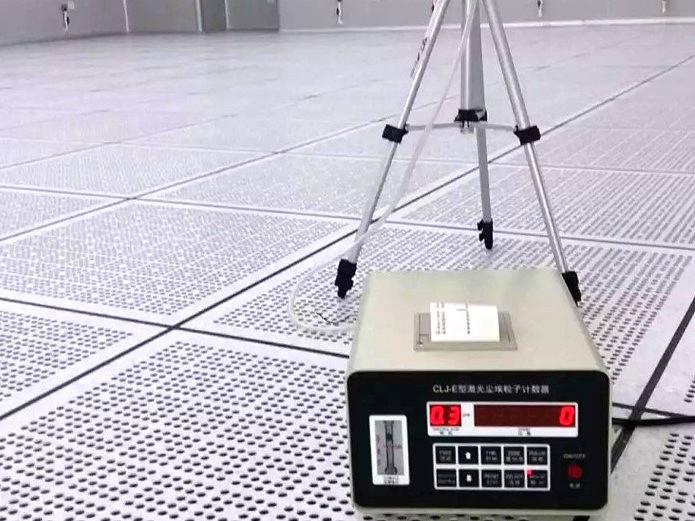
GMP araudia betetzeko, farmazia-ekoizpenerako erabiltzen diren gela garbiek dagozkion kalifikazio-eskakizunak bete behar dituzte.Hori dela eta, ekoizpen-ingurune aseptiko hauek monitorizazio zorrotza behar dute ekoizpen-prozesuaren kontrolagarritasuna bermatzeko.Funtsezko monitorizazioa behar duten inguruneek, oro har, hauts-partikulen monitorizazio-sistema multzo bat instalatzen dute, hau da: kontrol-interfazea, kontrol-ekipoa, partikulen kontagailua, aire-hodia, huts-sistema eta softwarea, etab.
Etengabeko neurketa egiteko laser hauts partikulen kontagailu bat instalatzen da gako-eremu bakoitzean, eta eremu bakoitza etengabe kontrolatzen eta lagintzen da lan-estazioko ordenagailuaren kitzikapen komandoaren bidez, eta kontrolatutako datuak lan-estazioko ordenagailura transmititzen dira eta ordenagailuak txosten bat bistaratu eta igor dezake. operadoreari datuak jaso ondoren.Hauts partikulen lineako monitorizazio dinamikoaren kokapena eta kantitatea hautatzea arriskuen ebaluazioaren ikerketetan oinarritu behar da, eta funtsezko arlo guztiak estaltzea eskatzen du.
Laser hauts partikulen kontagailuaren laginketa-puntua zehazteak sei printzipio hauei egiten die erreferentzia:
1. ISO14644-1 zehaztapena: noranzko bakarreko fluxuaren gela garbi baterako, laginketa-atatuak aire-fluxuaren norabideari begira egon behar du;Norabide bakarreko fluxuaren gela garbi baterako, laginketa-ataka gorantz begiratu behar da eta laginketa-abiadura barruko aire-fluxuaren abiadura ahalik eta hurbilen egon behar du;
2. GMP printzipioa: laginketa-burua lan-altueratik eta produktua agerian dagoen tokitik gertu instalatu behar da;
3. Laginketa-kokapenak ez du eragingo produkzio-ekipoen funtzionamendu arruntean, eta ez du eragingo ekoizpen-prozesuko langileen funtzionamendu arruntean, kanal logistikoan eragitea saihesteko;
4. Laginketa-posizioak ez du kontaketaren akats handirik eragingo produktuak berak sortutako partikulen edo tanten ondorioz, neurketa-datuak muga-balioa gainditzea eraginez, eta ez du partikulen sentsoreari kalterik eragingo;
5. Laginketa-posizioa gako-puntuaren plano horizontalaren gainean hautatzen da, eta gako-puntutik distantzia ez da 30 cm-tik gorakoa izan behar.Likido zipriztinduta edo gainezka badago posizio berezi batean, eta ondorioz, neurketa-datuen emaitzek maila honetako eskualdeko estandarra gainditzen dute ekoizpen simulatutako baldintzetan, norabide bertikaleko distantzia mugatu egin daiteke.
6. Saiatu laginketa-posizioa edukiontziaren igarobidearen gainean zuzenean jartzea saihesten, edukiontziaren gainean nahikoa airerik eta turbulentziarik ez sortzeko.
Puntu hautagai guztiak zehaztu ondoren, simulatutako produkzio-ingurunearen baldintzetan, erabili laser-hauts-partikulen kontagailua minutuko 100L-ko laginketa-fluxua duen eremu gako bakoitzean puntu hautagai bakoitza 10 minutuz probatzeko eta guztien hautsa aztertzeko. puntu partikulen laginketa datuen erregistroa.
Eremu bereko hainbat puntu hautagairen laginketa-emaitzak alderatu eta aztertzen dira arrisku handiko kontrol-puntua ezagutzeko, puntu hori hauts-partikulen kontrol-puntua laginketa-buruaren instalazio-posizio egokia dela zehazteko.
Argitalpenaren ordua: 2023-09-09